Iron ores are the most important and major raw materials for pellet production. pellet; It means the pellets produced from soft iron ore and other additives which are first raw and then cooked and hardened and used for regeneration using the traditional method of iron production in blast furnace or multiple methods of direct regeneration. The pellet is the primary material for the production of pig iron and it must have favorable mechanical, chemical and thermal characteristics in the reduction furnaces. To produce raw pellets, iron ore slurry including additives with wetting solutions such as water to achieve a spherical shape are rotated in pellet making machines to produce raw pellets. During the production of raw pellets, additives and adhesives such as calcium hydroxide may be added to increase the quality and mechanical metallurgical characteristics of the pellets. At this stage, pellets with desirable dimensions and sufficient mechanical strength are produced and sent for transportation to the baking machine. In the second stage, the raw pellets are carefully heated in a device below the softening temperature of iron ore in order to harden them in an oxidizing atmosphere, so that they are first dried and then baked, so that their porosity does not decrease.
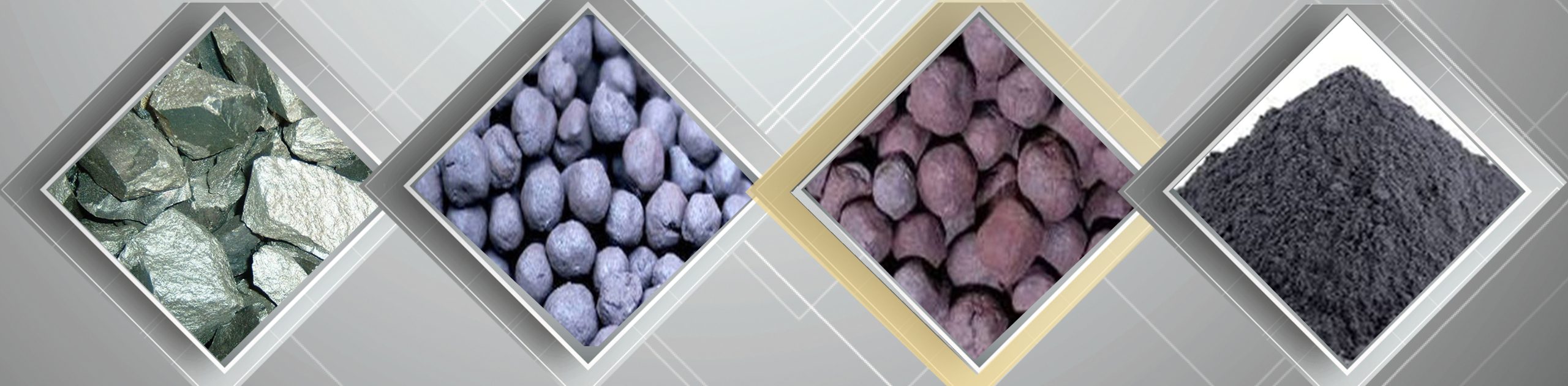
The mechanical and physical properties of pellets are important in the sense that pellets must withstand considerable mechanical loads during transportation, drying and hardening at high temperatures. Therefore, they must have sufficient wear resistance and compressive strength against crushing. Based on the uses of pellets, their necessary characteristics differ. To achieve these characteristics, special additives are used. Likewise, the machine used to produce pellets must be able to provide the necessary properties. The method of transferring them to the baking unit should be designed in such a way that the minimum impact and stress is applied to the pellet.
In the pellets used in the blast furnace or in direct regeneration methods, there are changes in the regeneration process that may cause them to crumble and disintegrate, so checking the mechanical and physical properties of the pellets and their regeneration is very important. It is necessary to carry out tests to determine the pellet properties under standard conditions.
The quality of pellets depends on their chemical, mechanical and metallurgical properties. Each of the properties are effective in the process of pellet production, regeneration, as well as smelting and refining of sponge iron and pig iron.
Physical properties of pellets
Among the determining factors of pellets are their dimensions, shape, specific surface area, dimension distribution, porosity, resistance to wear and friction.
1- Dimensions of the pellet
Pellets are divided into three groups according to size:
– Small ball with a diameter of 3 to 8 mm for agglomeration and hydrometallurgical process
– Normal pellets with a diameter of 10 to 15 mm for use in blast furnaces and direct regeneration units
– Large pellets with a diameter of 20 to 30 mm for use in steelmaking and raw materials for cement production
2- Pellet porosity
Porosity is one of the special properties of pellets and plays an important role in all stages of pellet making and consumption. In raw pellets, porosity is the result of uniform removal of water and its evaporation. The porosity in the pellet is very effective on the regeneration property. By increasing the porosity, the regenerative property of many pellets increases under certain conditions. On the other hand, the porosity is inversely proportional to the pellet strength, and its increase causes the pellet strength to decrease, so the optimal mode should be selected in adjusting these two factors. Porosity depends on particle size and pelletization method and plays an important role in drying and cooking. During these stages, the moisture evaporates and phase transformation occurs, and the materials re-crystallize. Considering the necessary strength, the best porosity of pellets is about 20 to 30%. The total porosity of the pellets is defined as the volume of the holes relative to the total volume of the raw pellets and is calculated using the difference between the actual and apparent specific gravity.
