Silicomanganese, which is also known as ferrosilicomanganese, is one of the ferroalloys used in the steel industry. Ferrosilicomanganese is an iron-bearing alloy produced by melting manganese ore and quartzite in the presence of coke in an electric arc furnace. Silicon and manganese are used in iron and steel as deoxidizers and to regulate chemicals. As its name suggests, this ferroalloy is a combination of silicon and manganese. The furnace used in the production of percarbon ferromanganese is also used to produce this category of ferroalloys. The production process of ferrosilicomanganese is much more difficult than that of ferromanganese. The main reason is that a higher temperature is needed to reach the desired amount of silicon. Usually, the slag produced in the production of high-carbon ferromanganese is used for the production of ferrosilicomanganese. In this way, ferrosilicon manganese is produced from the combination of slag with high manganese oxide, which contains 35% to 45% of manganese oxide, manganese rock, quartz and coke.
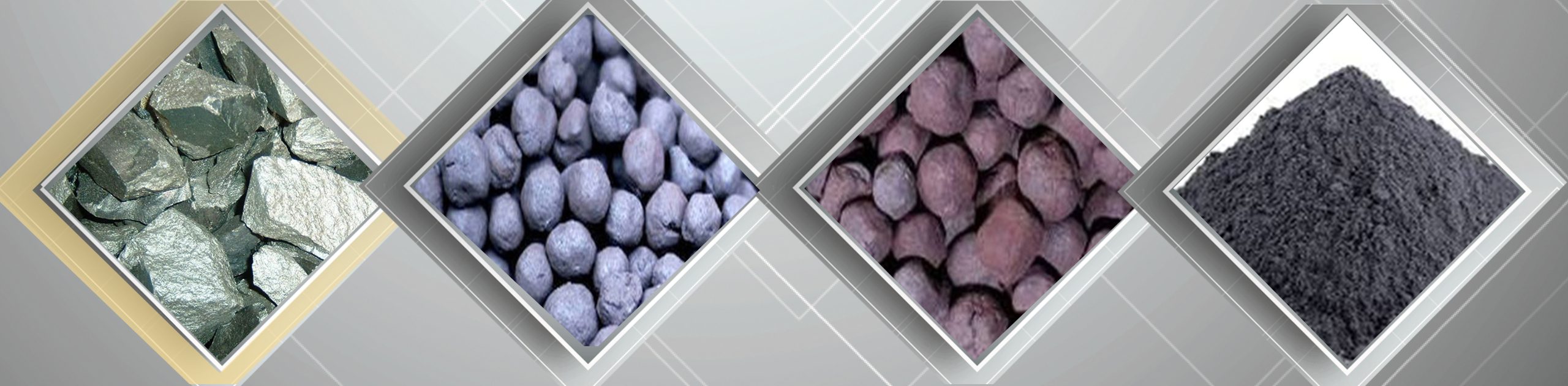
Standard ferrosilicomanganese contains 70% manganese, 18% to 20% silicon, and 10% iron, and typically contains 12 to 16% silicon and 50 to 70% manganese. Silico-manganese is used in steelmaking for deoxygenation, desulfurization and improving the mechanical properties of steel through the addition of alloying elements. Today, economic efficiency as well as maintaining the composition of the melt has increased the tendency of steelmakers to use silicomanganese instead of a combination of ferrosilicon and ferromanganese. According to the latest information, after ferrochrome, silico-manganese has the largest share in the production of ferroalloys. Of course, as is the case with other ferroalloys, access to raw materials as well as energy costs have made imports the source of demand for many countries.
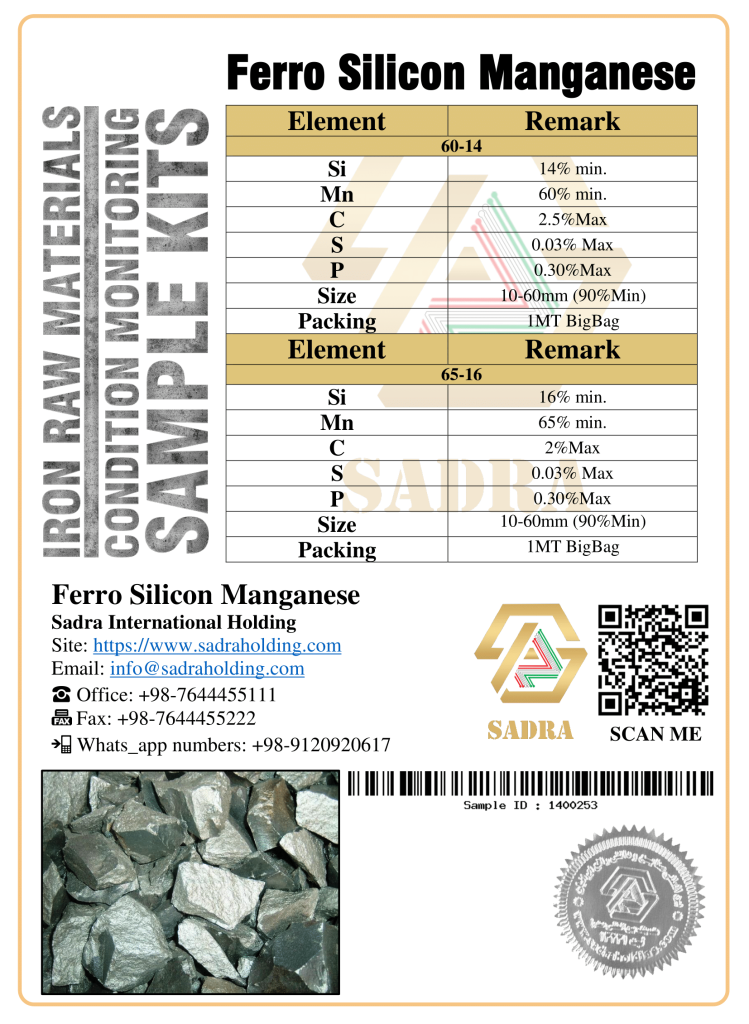