Silicon is the most abundant element in the earth’s crust after oxygen and is usually found in nature in the form of quartz. Today, silicon has been used in various industries, but one of its alloys that has been widely used is “Frosilis”.
Ferrosilicon is an alloy of iron and silicon produced by heating, reduction and melting of iron ore and silica (quartz) by carbon, mainly in electric arc furnaces. Its composition ratio is mainly from 10 to 90 percent of silicon and the rest is iron. At the same time, impurity elements such as manganese, iron, phosphorus, sulfur and aluminum can be present in ferro-silica in amounts less than 0.5%. Carbon is present as an impurity (unwanted) and also as a third element in all types of ferrosilices.

The biggest consumers of ferrosilica are steel factories. Foundries are also other consumers of this material.
Ferosilis is one of the amigants used in various industries, especially metallurgical industries, and in this sense, it is very important. How this material is used in the industry depends to a large extent on the ratio of iron and silicon in it, as well as conventional impurities.
Ferrosilicon can be used in metallurgical industries as an alloying, nucleating and deoxygenating element, and almost pure silicon can be used in electronic industries as a semiconductor and rectifier.
In addition, the combined derivatives of silicon are used in the production of siliceous resins, glazes, rubber, etc.
Reducing agent in the production of other ferroalloys:
When ferrosilicon is used in steel casting, its strength, hardness, elasticity and magnetic ability increase. By adding ferrosilicon to the melt, it is also possible to prevent the formation of unwanted carbides.
Ferrosilicon and ferromanganese are two widely used ferroalloys in steelmaking industries.
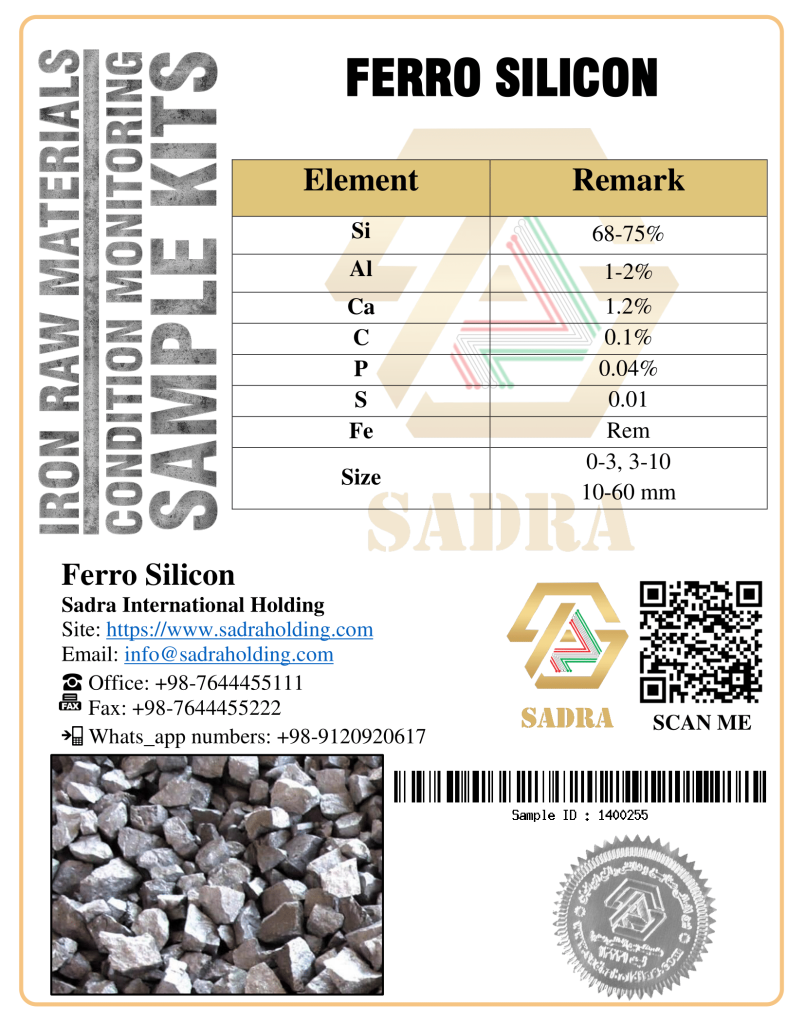