Sponge iron is a high-quality source for iron and steel production, which is obtained from the recovery of natural or processed iron mineral without reaching the melting temperature. In this method, iron ore pellet which has a grade of 67% is regenerated and the result is sponge iron (porous pellet) with about 92% Fe. The product of the regeneration unit is transferred to the steelmaking department for direct charging of the furnace without going through the cooling part in the furnace and with a temperature of about 600 degrees Celsius.
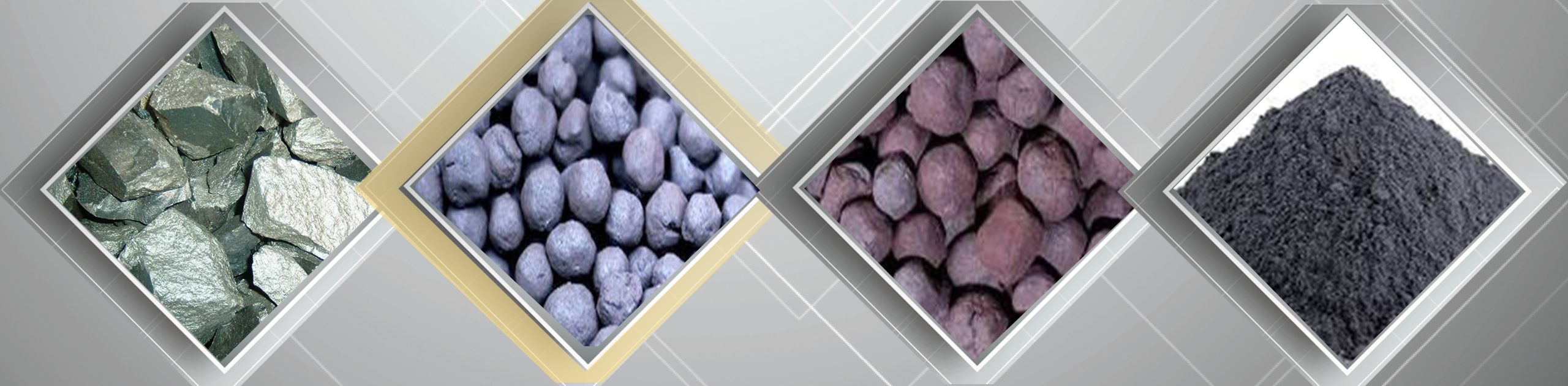
Sponge iron, after melting and regeneration in steelmaking, is used in the casting process in the form of products such as slabs, billets, and rebars. Today, about 5% of the world’s steel is produced from sponge iron, and this trend is increasing.
Sponge iron is obtained from the direct reduction of iron ore and is also called DRI.
Application of sponge iron
The application of sponge iron in induction furnaces is one of its most important applications. It can be said that the use of sponge iron in induction furnaces is able to replace scrap iron by nearly 50% and also the use of sponge iron is a big change in continuous casting (CCM) of the steel industry.
It can be used in almost all steel production methods. Many small and large steel production units in the country use these methods. Iran has more available natural resources for direct restoration. Sponge iron is a suitable substitute for iron waste, so we can supply a high percentage of raw materials to meet the melting requirements of steelmaking units, instead of using waste, through sponge iron.
Direct recovery of iron ore is done through gas or coal sources. The selection of the direct recovery method of iron ore depends on the location of the production plant and the available resources. For example, in Iran, despite the rich gas resources, choosing gas resources is a more reasonable choice and gas is used as a regenerative substance. As you know, the use of coal resources for regeneration also leads to air pollution problems, and accessing its mines is not an easy task, but currently the largest producer of sponge iron in the world is India, which uses coal resources. he does.
